Pre- Sale.
We can customize the machine according to the material sample send by clients. We have experienced engineers who will analysis the source first, design the machine and match the proper catalysts according to the test result and maximize the value of output products.
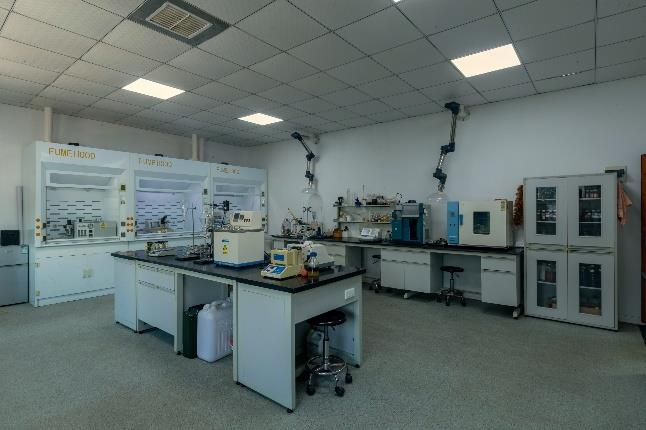
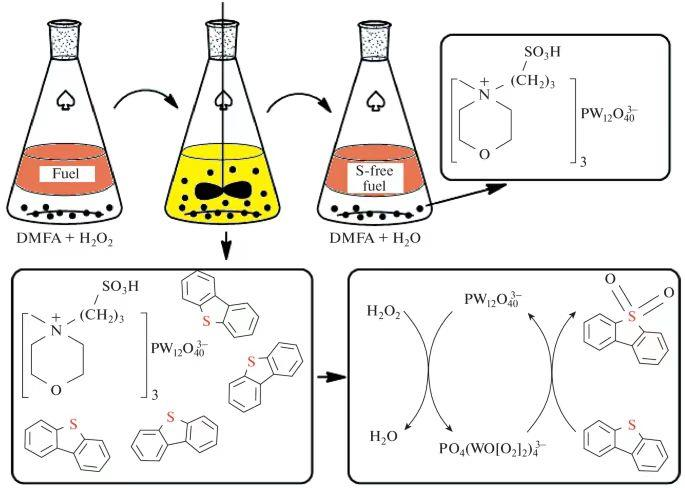
1.The raw material must be analysed first to determine the production process and catalyst used to achieve the best result. Different materials have different oil yield depends on the contents.
2.Communicate and understand your need for final product to provide the most cost efficient and productive design.
3.Lab production test and feedback.
4.Modification and details discussion about heating method, furnace material, optional equipment for gas emission, desulfurization and bleeching etc.
5.Customize electrical equipment and controlling method(Manual, semi manual, PLC, SCADA).
6.Finalize the contract and ready to produce.
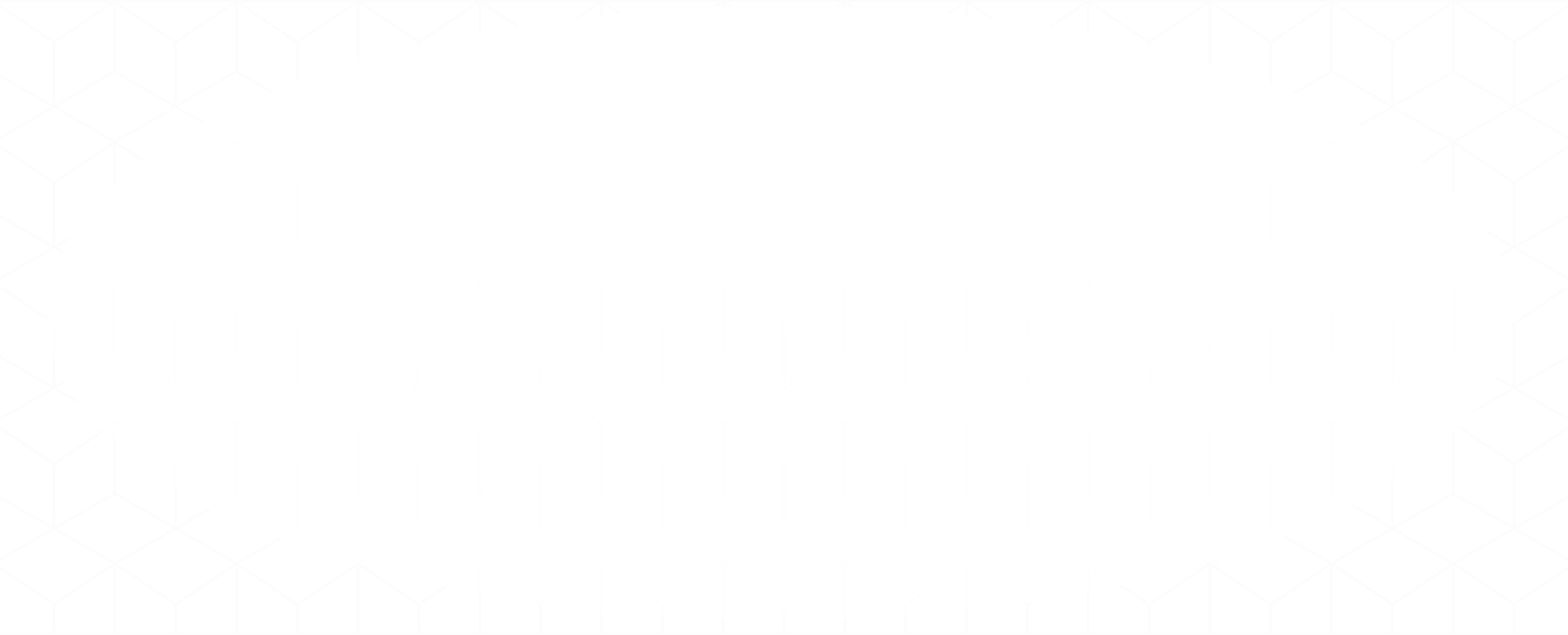
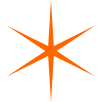
After-Sale.
Our after-sale team will track the production process and report to the client in a regular basis. After the delivery, our engineer will guide the installation and test running until the local workers can operate independently.
We have one year guarantee on the major parts, replacement accessories are available to order any time. We also have a fast response customer service available for your need, problems will be recorded and solved on time.
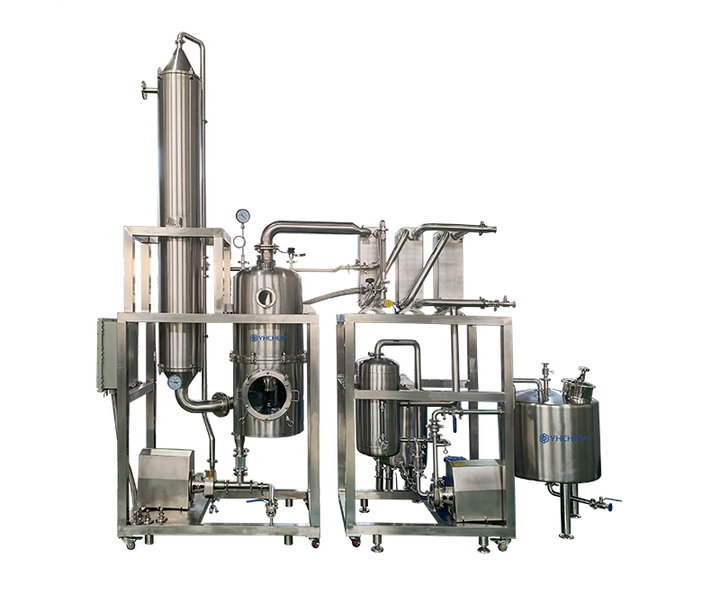
1.Order the high quality material and start manufacturing, email update with client each week.
2.Manufacturing according to schedule and finish on time.
3.Send the equipment to clients .
4.Dispatching our support team to help the client for plant installation, adjust and test equipment on site before it put into operation.
5.Tutoring the local worker until they can operate independently.
6.Lifespan in time hotline service for technical issues and accessories orders.
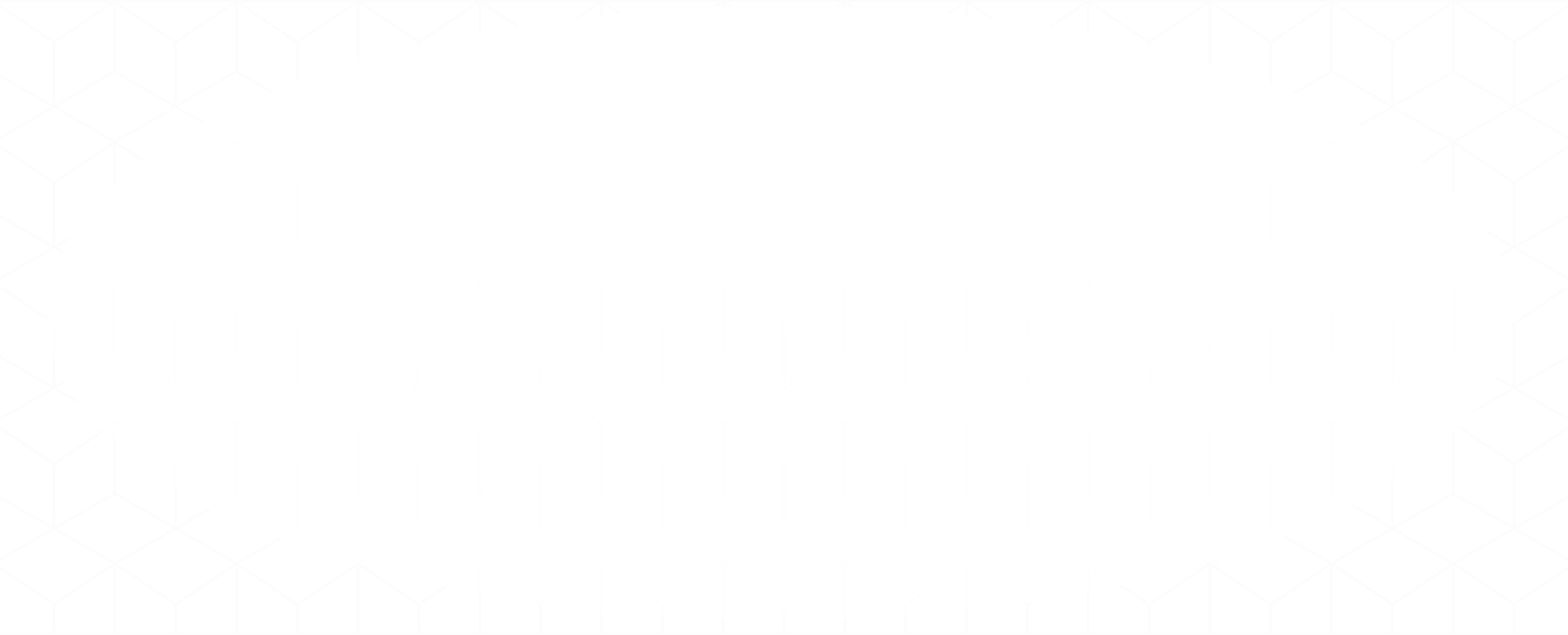
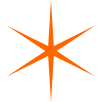